Alright, let’s talk about this pneumoisa relay setup I finally wrestled into working. It wasn’t exactly straightforward, took a bit of messing around in the workshop.
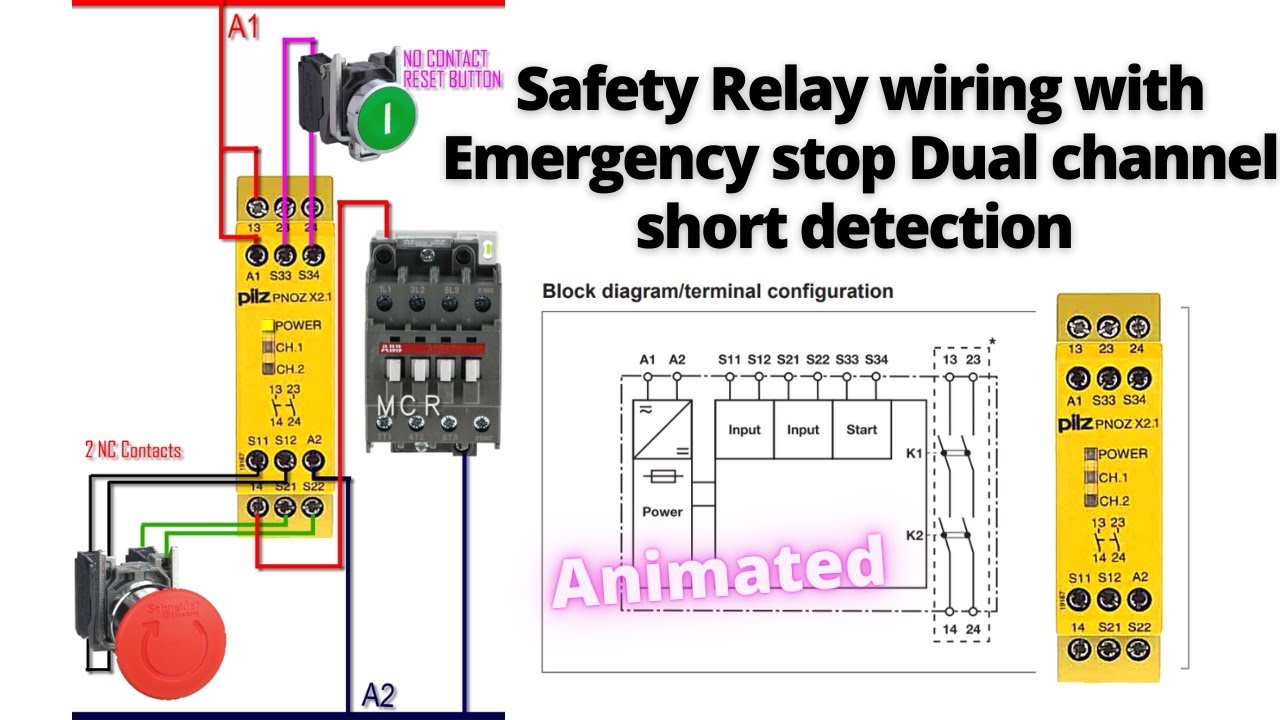
So, the whole idea started because I got tired of manually switching things. I had this pneumatic clamp, right? And I wanted it to activate automatically based on a signal from another machine finishing its cycle. Sounds simple, but making different bits of gear talk to each other when they weren’t designed to… well, that’s where the fun starts.
Getting the Signal Right
First thing was tapping into the ‘finished’ signal from the main machine. It wasn’t a nice clean digital output, more like a voltage drop on an auxiliary line. Had to figure out the right threshold. Spent a good afternoon with a multimeter just watching the damn thing cycle, writing down voltages. Felt like old times, squinting at readings.
Then, needed something to act on that signal. I dug out an old industrial relay I salvaged ages ago. Big clunky thing. Tested it on the bench, still worked fine – you get that satisfying thunk when it switches. But interfacing that voltage drop to trigger this hefty relay needed a bit of electronic glue.
I tried a couple of approaches:
- First attempt was a simple transistor switch. Worked, kinda, but was super sensitive to noise. The main machine starting up would sometimes false trigger it. No good.
- Then I thought, maybe an opto-isolator? Cleaner signal separation. Wired one up. Better, much better. Less random clicking from the relay.
Connecting the Air Part
Okay, electrical signal triggering the big relay was sorted. Now, the ‘pneumo’ part. The relay’s job was to switch the power to a solenoid air valve. This valve controls the air going to the clamp. Simple enough, right? Just wire the valve’s power through the relay contacts.
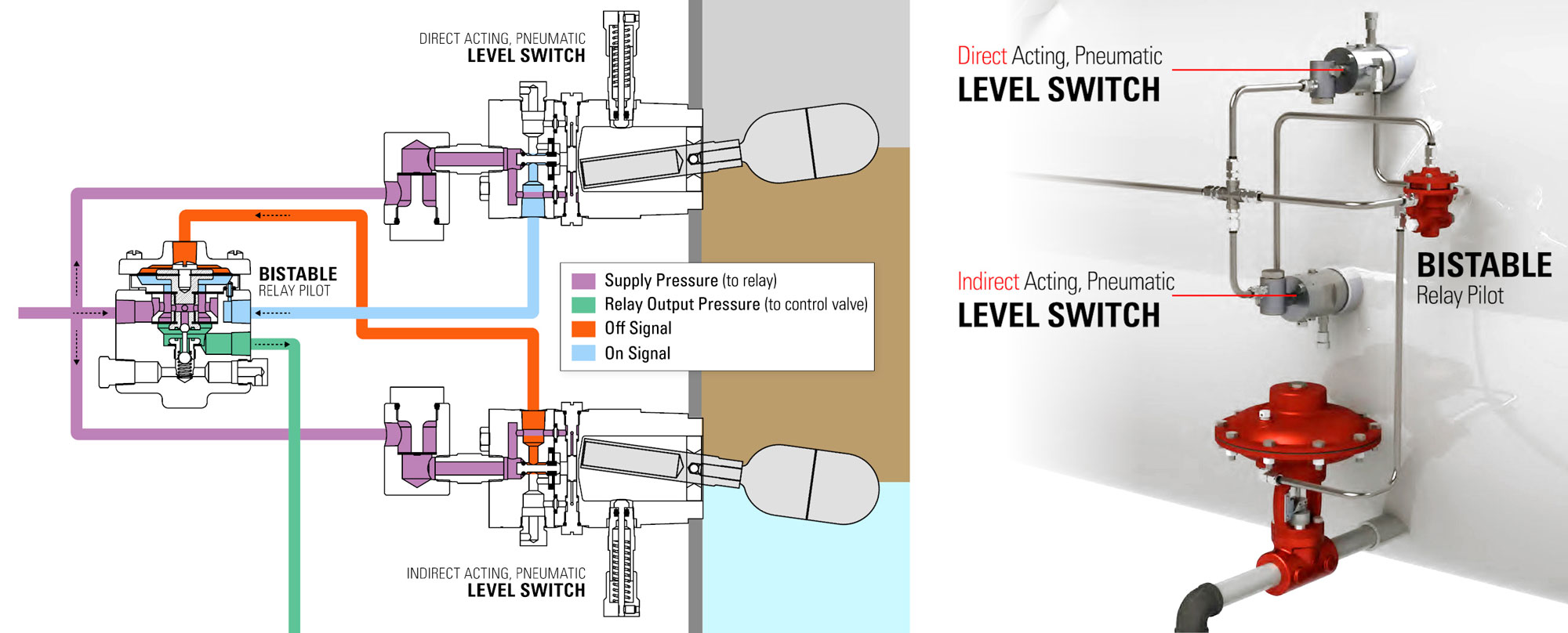
Did that. Powered everything up. Machine finishes cycle, voltage drops, opto-isolator triggers the relay, relay thunks, solenoid valve clicks… but the clamp barely moved. Weak. Checked the air pressure, it was fine. Took me a while to realize the solenoid valve itself was gummed up. Probably from sitting in a box for years. Had to take the darn thing apart, clean the gunk out with some solvent, put it back together. Always the simple things that trip you up.
Putting It All Together
So, after cleaning the valve and properly shielding the signal wire from the machine (just wrapped it in some foil tape, nothing fancy), it finally started behaving. Machine finishes, signal drops clean, relay kicks in reliably, valve opens fully, and snap, the pneumatic clamp engages hard and fast like it’s supposed to.
It’s running now. Does the job. Took maybe a day longer than I expected, mostly fiddling with that signal sensitivity and then discovering the sticky valve. But hey, that’s how these little workshop projects go, isn’t it? You fix one thing, find another. Feels good when it finally clicks into place, though. Solid bit of automation, saved me a button press. Worth it.